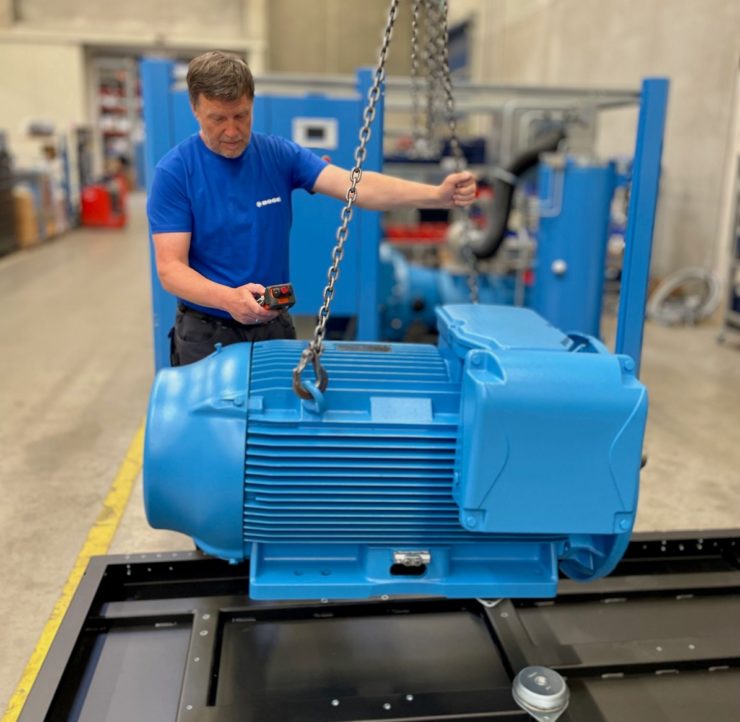
Courtesy of BOGE
Improved efficiency ratings and an extra boost in effective free air delivery for industrial, healthcare, and food manufacturing, including domestic applications.
November 8, 2022: Designed to take the lead, BOGE’s already efficient S-4 series compressors have now become even more efficient. The compressor and compressed air systems manufacturer is replacing the existing IE3 motors in its current 110 kW – 160 kW screw compressors with high-performance, energy-saving IE4 motors. In addition to the energy benefits, users will also enjoy lower future CO2 emissions, long-lasting operations, and low maintenance costs.
Applications involving electric motors make up a huge proportion of the overall energy used in the industrial sector. In order to drive the environmentally compatible design of electric motors, promote sustainability and minimise CO2 emissions, the European Union has specified a series of minimum requirements for energy efficiency in three-phase asynchronous motors. Consequently, all motors with an output between 75 kW – 200 kW will be required to have an energy efficiency rating of IE4 from July 2023 onwards.
“All screw compressors in the lower performance classes will be modified over the coming months to ensure that BOGE remains ahead of all legal requirements when it comes to the more efficient, environmentally friendly IE4 motors,” says Nalin Amunugama, General Manager, BOGE Kompressoren Asia Pacific.
IE4 motors as standard
The energy efficiency of an electric motor is a measure of the ratio between the mechanic power output and the electrical power input. There are currently a total of 5 international energy efficiency classes (IE), which are determined according to standardised measurement procedures, with motors in efficiency class IE1 being the least energy efficient.
“The IE4 motors used to be available as an optional extra in our S-4 series, but they’ll now be available as the standard,” explains Nalin. “Our aim is to achieve energy savings of between 0.6 and 1.5 percent.”
Companies with energy costs in the six figures will find the savings considerable. To illustrate the point – for a 110 kW compressor operating for 8,000 hours/year, a reduction in electricity consumption of around just 1 percent will result in yearly savings of €1,500 (USD1,481).
Although the changeover to IE4 motors does not affect the overall dimensions of the screw compressors, it certainly improves the effective free air delivery, as this can also be increased by up to 1.6 percent. Ultimately, by using more efficient motors, BOGE is not only helping to reduce its customers’ electricity bills but will also be making a significant contribution to fighting climate change, thanks to the reduced CO2 emissions coming from its devices.
Improving the efficiency of motors and motor-driven systems, therefore, plays an important role in reducing ownership costs and slowing electricity demand growth. Doubling the efficiency of new industry motor systems worldwide could reduce CO2 emissions in 2030 by more than a gigatonne.
Governments use IE standards to specify the efficiency levels for their minimum energy performance standards (MEPS), as well as other policy measures. Of the 57 countries that currently have mandatory industrial motors MEPS, 45 of these, including Singapore, are at the IE3 level. The European Union, Norway, Switzerland, Turkey, and the United Kingdom are transitioning to IE4 levels in 2023 for motors in the 75-200 kW range.