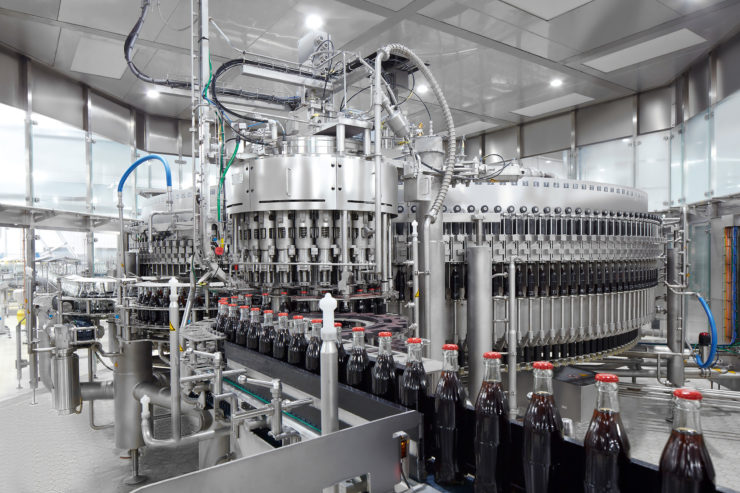
Courtesy of KHS
In a span of just three years, Coca-Cola in Germany has invested around 50 million euros in one of its biggest plants in Mannheim. KHS has contributed a returnable glass line to the project – one that also manages highly complex sorting tasks.
In July 1950, beverage retailer Wilhelm Müller procured bottling rights for Coca-Cola in Germany. He established the entrepreneurial basis for the production site, which is still present in Mannheim. Initially, lots of tasks, such as sorting and quality assurance, were performed manually until 1965, when the first fully-automatic setup went into operation. This lifted empty bottles from the beverage crates, placed full ones back into the same, and automatically inspected every single container with the help of test equipment.
In the 1960s and 1970s, Müller held the sales record of all independent Coca-Cola franchisees in Germany for 18 years in a row. Following his death at the height of his success in 1971, his wife took over the running of the business. In 1983 she then made the bold decision to build a completely new factory – at the present location in Mannheim-Vogelstang. Very soon after its opening, over 30,000 bottles per hour were being filled on new plant engineering.
High-tech in Mannheim
Today, the production plant is part of Coca-Cola Europacific Partners Germany (CCEP DE), the biggest beverage producer in the Federal Republic. “Among our older employees, there are still plenty who fondly look back to what’s known as the Cola Müller era,” smiles Christopher Bee. The 39-year-old has worked in Mannheim for seven years and was made plant manager in September 2021. The extensive company premises still belong to the Wilhelm Müller Foundation, with the lease extended for another 30 years just two years ago. “There’s nothing old-fashioned about our technical equipment, however,” he grins. “In 2018 and 2019, we invested around 50 million euros in two new filling lines. These were the biggest investments ever to be made in the history of our production site. This makes us here in Mannheim one of the most technically advanced Coca-Cola plants in Germany and Europe.”
One of the two new production lines is a returnable glass system from Dortmund systems supplier KHS. “We fill a total of six different bottles on this line: four in 200-milliliter and two in 330-millilitre format. The smaller sizes are primarily destined for the hospitality trade, where the packaging has to be more impressive than retail. This is why the Coca-Cola, Fanta, Sprite, and mezzo mix brands on this line have their own respective bottle designs. We process two formats for the bigger containers that are also sold in the retail trade: what’s known as the contour bottle for products in the Coca-Cola family and our green multi-bottle for Fanta, Sprite, and mezzo mix.”
One outstanding feature of the KHS line is the sorting system that can feed the empty bottles by type to the washing and filling process fully automatically. “In principle, the sorting and filling processes occur on two separate systems. We use a segment to combine both sections specifically for our main product types, the 200- and 330-milliliter Coca-Cola bottles. Here, the containers largely returned from the market by type are sent straight from sorting to production. They no longer have to take a detour through the empties warehouse. This reduces the amount of effort needed for handling.” The other five product types from the sorting process are first packed into beverage crates and then onto pallets before being temporarily stored until they are filled.
Intelligent decrater
Thanks to the system’s high degree of automation, the only manual task required takes place right at the start of sorting. When the crates arrive, they’re scanned from above. If they contain foreign objects such as paper cups or film, the crates can’t be identified. The obstacle must be removed by hand before the crate can be fed back into the automatic process. “The decrater is so intelligent that it places the biggest bottle type on one conveyor,” explains Bee. “The smaller bottles are set down on a different conveyor where they’re separated and guided to different lanes with the help of camera systems and pushers. Here, we aim to manipulate the containers as little as possible: in other words, to ensure that they have very little contact with the machine. In this way, we can keep the risk of something falling over at such high speed to a minimum.” With an output of up to 66,000 bottles per hour, the sorting system has a greater capacity than the returnable glass line that can fill a maximum of 60,000 bottles every 60 minutes. This means that CCEP in Mannheim seldom suffers any downtime with its empties – even during the peak season.
Great flexibility
The irregular return of empties often results in peaks, says Bee. One good example is music festivals, at the end of which more empty glass bottles are to be expected than usual. “What’s special about this system is that it can individually react to these peaks,” he states. “To facilitate this during commissioning, we ran a live simulation with an external service provider. Based on the results, in close cooperation with KHS, we were then able to make several optimizations and fine adjustments to the layout that improved performance. This was extremely helpful, especially as we couldn’t work under real-life conditions during the pandemic due to closures in the hospitality trade.”
For Christopher Bee, one highlight of the new returnable glass line from KHS is the Innoclean DM double-end bottle washer. “On average, we save up to 40 percent in water and energy for each filled bottle compared to previous-generation systems,” Bee emphasizes. This is enabled by freshwater control. For instance, that’s automatically adjusted to the current machine capacity by a control valve. The new ECO carriers are also good for the energy balance: they weigh about a quarter less than the previous bottle pockets and have side openings that permit better rinsing. This reduces the amount of caustic and heat carryover and thus the cooling requirement within the machine. If no empties are available at any point, the bottle washer switches to an energy-saving idle state: its new standby mode. To this end, the Liquid Efficiency Spraying System (LESS) lowers the pressure of the spray pumps to 0.3 bar during downtime, thus cutting electricity consumption by up to 80 percent.
All set for net zero
As in an increasing number of companies, the issue of sustainability plays a big role at CCEP. By 2030, Europe’s greenhouse gas emissions will drop by 30 percent compared to 2019. By 2040, CCEP wants to reach its net zero emissions target and have no more impact on the climate. Not only the emissions from its main line of business are accounted for here. Rather, significant areas of potential for reducing greenhouse gas emissions are being sought throughout the entire value chain. This includes investing in an energy- and resource-saving machine park and fully converting the company’s 2,300 service and commercial vehicles to electric drives by 2025. Coca-Cola in Germany avoids further emissions with its close-knit production and distribution network that manufactures and supplies beverages on a mostly regional basis. Where this isn’t possible, the beverage producer is relying more and more on the railroad. In 2021, a freight network was set up with DB Cargo that links 13 sites with one another, allowing 1.7 million truck kilometres and 1,000 metric tons of CO2 to be saved in the same year.
Coca-Cola and KHS: successful cooperation at several sites
Within the Coca-Cola network, Mannheim is the most recent of three major projects for more climate-friendly production that KHS has implemented with CCEP Germany in the last few years. A canning line for Karlsruhe about 70 kilometres away marked the start of the undertaking in 2015. “This line with its capacity of up to 120,000 cans per hour is convincing with our resource-saving tunnel pasteurizer, for example,” says Robert Fast, project manager at KHS. “It uses water collected from the empty can rinser. And the use of ionized air in the process water enables the amount of chemicals to be reduced compared to the standard process.” The packaging machine is just as climate-friendly, he adds; the gas burner in the shrink tunnel cuts the consumption of electrical energy by up to 75 percent and carbon emissions by up to 60 percent.
In 2017 KHS installed a non-returnable PET line with a capacity of up to 42,000 bottles per hour in Mönchengladbach on the Lower Rhine. “One of the reasons we won the contract was our extensive electricity-, water- and gas-saving concept,” Fast reports. “One example of this is the InnoPET Blomax stretch blow moulder. The near-infrared or NIR technology of the heater, where the preforms are heated upstream of the actual stretch blow moulding process, cuts the amount of energy needed.”
Christopher Bee, of course, also knows that investments of this magnitude are not the rule. Thus, he considers himself lucky that he’s been able to experience this at ‘his’ plant. “To see how a production site develops to represent the entire production range is something really special,” he says happily. “It’s, of course, clear that we’ll return the trust placed in us in the form of extremely good performance.” ‘Cola Müller’ would have undoubtedly echoed this sentiment.
At a glance: Coca-Cola Europacific Partners
With 33,200 employees and 1.75 million customers in 29 countries, Coca-Cola Europacific Partners (CCEP) is one of the world’s leading consumer goods companies. The beverage bottler produces and sells popular beverage brands such as Coca-Cola, Fanta, and Sprite in Europe, the Pacific, and Indonesia. CCEP Deutschland GmbH is part of CCEP, and with a sales volume of over 3.5 billion litres (2021), it is the biggest beverage company in Germany. The bottler employs around 6,500 people throughout the Federal Republic. For more information, go to: www.khs.com/en/media