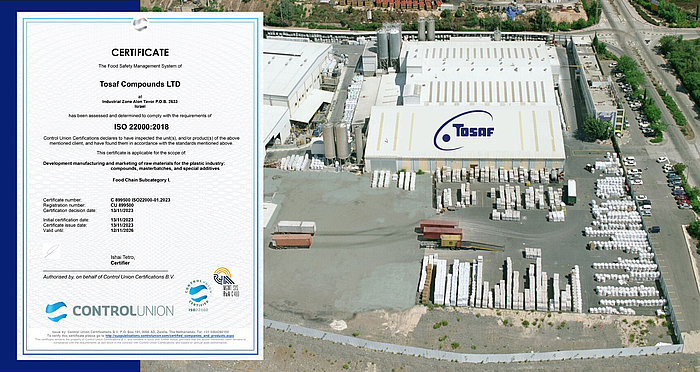
Courtesy of Tosaf
To further strengthen the trust of business partners and customers in the global food packaging industry, the safety management of Tosaf’s production facilities for white and additive masterbatches has recently been certified to ISO 22000. This globally recognised key standard comprises strict specifications, including production and processing, transport, storage, and labelling of products used in the food industry. The company has already been certified in accordance with international quality standards such as ISO 9001, ISO 14001, and ISO 45001.
As a company that has always focussed on the needs of its end customers, Tosaf has decided to take this voluntary step. With this current certification, which includes continuous monitoring and documentation as well as preventive measures to minimise risks, the masterbatch manufacturer is now one of the few of its kind in the world to make this additional contribution to health protection along the entire food chain.
As part of the requirements of ISO 22000, Tosaf utilises the most advanced computer technologies and control systems to ensure maximum quality and safety as well as complete traceability of its products. The numerous safety measures range from the particularly critical selection and regular review of suppliers as well as strict incoming raw materials inspections up to product release. They also include particularly careful selection of personnel and strict access controls to the production facilities.
Tosaf provides detailed documentation on the substances contained in the white and additive masterbatches it delivers. It declares conformity with the relevant regulations and helps its customers, mainly manufacturers of food packaging, including films, injection, and blow-moulded parts such as yoghurt pots, bottles, etc., to document their own company’s fulfilment of the strict regulations.
As Dina Khomchuk, Q&A Manager for Tosaf’s Additives Business Unit, explains: “Tosaf places great importance on supplying the food industry with high-quality raw materials that meet the strictest requirements. As part of the new ISO 22000 certification, including ISO 22002 Part 4, which is specifically tailored to food packaging, we have comprehensively adapted our processes to this area of application and optimised them even further. We have developed a multi-year plan that includes measurable goals in the areas of quality, food safety, and environmental quality. We allocate resources and train the entire organization in food safety. On this expanded basis, Tosaf is looking forward to growing in the market for masterbatches for food packaging.”
Broad product portfolio for food packaging
The majority of Tosaf’s additives and white masterbatches are intended for the food packaging sector, where they enhance the performance and safety of the materials used. In addition to extrusion, including the production of multilayer and BOPP films as well as extrusion coating, injection moulding and blow moulding are typical processing methods for these products.
Tosaf tailors their exact composition to the specific requirements of the packaging material and the regulations for food contact materials in the intended market. As a long-standing partner in this industry, Tosaf has a deep understanding of the legal requirements and restrictions that apply there. This enables the company to make an important contribution to ensuring that the finished packaging complies with regulations and standards, e.g., those of the FDA and the EU, for direct contact with food.
Based on its extensive expertise in this area, Tosaf has developed its portfolio of functional additive masterbatches for the food packaging sector into one of the broadest in the world. In addition to a wide range of traditional additives, these include special, high-performance antifog additives, newly developed PFAS-free processing aids, the recyclable Matte Effect additive, which forms very thin layers on polyethylene films and combines superb haze with extremely low gloss, and the Permanent Slip antiblock additive, which ensures immediate and stable slip properties without affecting the corona treatment and the lamination process.
Tosaf’s high-quality white masterbatches withstand even demanding processing conditions and offer high dispersion quality and colour strength. In their respective versions, they take into account the specific requirements of individual applications, such as the organoleptic properties for milk packaging, the use of migration-inhibiting additives for applications such as lamination and metallisation, as well as the avoidance of die buildup and strong smoke and odour due to the high processing temperatures during extrusion coating.
For over three decades, Tosaf (https://www.tosaf.com/) has been developing and manufacturing high-quality additives, compounds, and Color masterbatches for the plastics industry. With the aim of providing for its customers’ every need, it has continuously grown and developed its offering, production capacity, and global reach, becoming a truly close to the market, global organization. Servicing customers in over 50 countries in Europe, North America, South America, Asia, and the Middle East, Tosaf has over 1400 employees spread throughout its production sites, warehouses, sales, and distribution offices around the world.
Tosaf’s major shareholders include: Megides Holdings Ltd. and the Ravago Group.