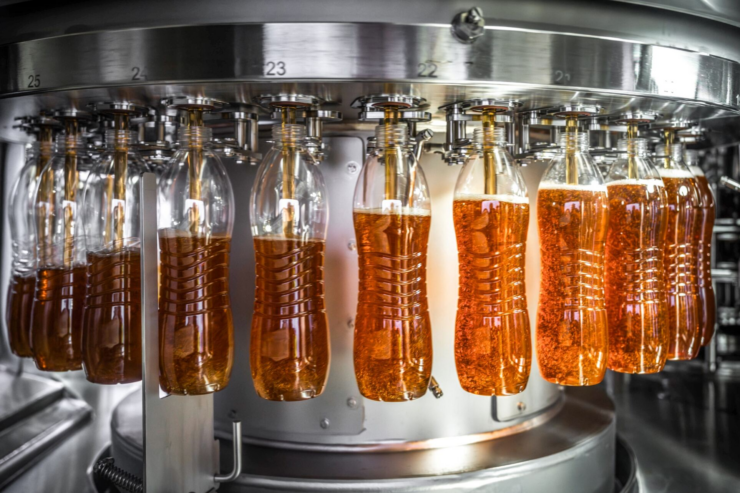
Courtesy of Sidel
In an exclusive conversation with Naima Boutroy, Global Packaging Technical Support at Sidel, we delve into the intricacies of beverage preservation that go beyond mere flavors.
At the heart of the beverage experience lies the nuanced interplay of texture and mouthfeel, aspects that are as crucial as taste itself.
Boutroy, a veteran in PET bottle development with tenure at Sidel since 1986, shares her profound insights on pioneering packaging solutions. Under her guidance, Sidel has embarked on a mission to not only safeguard the delicate balance of a beverage’s texture and mouthfeel but to do so through innovative, sustainable practices.
Sidel’s advancements are reshaping the beverage landscape. It ensures that each sip delivers an experience true to its intended essence, proving there’s more to beverages than meets the taste buds.
How is Sidel innovating in packaging materials to preserve texture and mouthfeel in beverages? Can you elaborate on any specific materials or technologies that are particularly effective?
PET is widely recognised as a packaging material that preserves beverages, their texture and mouthfeel.
To further extend the barrier performance of PET, Sidel has developed Actis (Amorphous Carbon Treatment on Internal Surface) a pioneering plasma coating technology. The coating is deposited inside PET bottles improving the protection of carbonated soft drinks (CSDs), beer and oxygen sensitive beverages like juices or teas, so it can increase shelf life while preserving its freshness.
In addition to our dedicated Actis technology, we work closely with our suppliers to utilize additives to create packaging options with advanced barrier features.
Sidel is also widely known for its expertise in aseptic technologies, traditionally used for beverages such as liquid dairy products, juices, nectars, soft drinks, isotonics, and teas. These products require a high level of care to preserve their organoleptic properties and extend shelf life.
Could you explain the role of barrier properties in packaging and how Sidel’s solutions enhance these properties to maintain the quality of beverages?
Packaging barriers preserve the product integrity and guarantee the nutritional and organoleptic properties of the beverage. Similarly, they prevent CO2 loss, avoid product oxidation and minimize water vapor escaping from the product – this all helps to preserve drink texture and mouthfeel. Barriers can also protect the product from the light to secure its quality.
Sidel has developed a suite of customised barrier solutions adapted for beverages, including:
The Actis plasma coating barrier technology can increase shelf life by up to seven times for carbonated products and thirty times for oxygen-sensitive beverages such as JNSDIT (juice, nectars, soft drinks, isotonic, and teas). Depending on the product type, bottle weight, and size, it can also improve the vapor water barrier by three times.
We also work closely with our suppliers to develop solutions:
- protecting against light for liquid dairy products using mono or multi-layer bottles and sleeves;
- within bottles with new additives for use on our aseptic equipment.
How does Sidel balance the need for sustainable packaging with the requirement to preserve beverage texture and mouthfeel? Are there any challenges or breakthroughs in this area?
At Sidel, we’re committed to ensuring packaging complies with new worldwide regulations, including the European Packaging and Packaging Waste Regulation.
“Our emphasis is on preserving product integrity while enhancing packaging circularity and reducing greenhouse gases.”
PET is already compliant with the circular economy, yet to reach carbon neutrality, lightweighting and recycled PET play an important part. At Sidel, when developing new packaging solutions that are 100 per cent compatible with rPET and utilise lightweighting to create sustainable bottles which offer a long shelf life and preserve texture and mouthfeel.
Sidel is also supporting beverage manufacturers to recyclable design packaging. In June last year, we launched our RePETable™ offer, the 360° one-stop shop for recycled PET, it supports secure bottle production efficiency and quality whatever the rPET resin percentage, and the industry in developing designs for recycling packaging.
With the RePETable™ offer, we’re committed to creating a virtuous closed-loop process for food-grade rPET bottles, which will help grow the market for recycled PET further in the future.
To establish a true closed-loop process for rPET bottles, this also means to design the primary packaging with the view of making it easily recyclable. Through our RePETable™ offer, we aim to support robust primary packaging circularity by helping the market innovate with new materials for primary packaging (closures, sleeves, glues, labels, additives and colouring…) while ensuring they are designed-for-recycling. For this, we leverage a unique asset, our small-scale PET recycling pilot line that recreates every step in the recycling process.
How does the shape and design of a package influence the preservation of a beverage’s texture and mouthfeel? Are there specific designs that Sidel recommends for certain types of beverages?
PET offers bottle manufacturers greater creative freedom to create iconic shapes. Importantly, elements of the bottle design, such as wall thickness, the sealing system, and bottle shape, ensure freshness and impact the beverage’s mouthfeel.
“At Sidel, we use our unique expertise to help producers identify the optimum wall thickness, neck size and bottle weight for their requirements.”
For aseptic applications, we can also advise on the most suitable sealing design. In addition, based on our long experience, we can also recommend the most suitable additives to PET bottles to further enhance barrier protection for oxygen and light and preserve CO2 content.
Can you discuss any innovative techniques or technologies Sidel is using or developing to extend the shelf life of beverages without compromising their texture and mouthfeel?
Sidel uses cutting-edge technology to help producers extend the shelf life of beverages without compromising on the mouthfeel. This is especially true within the aseptic drinks sector.
Unlike traditional methods, our Aseptic Combi Predis incorporates dry decontamination, ensuring the production of a commercially sterile product filled in a sterile environment, all within a sterilised package.
Sidel’s unique PET aseptic filling solution with dry preform decontamination ensures product integrity, production flexibility, cost efficiency, and sustainability.
Since it is simpler to decontaminate the preform rather than the blown bottle, Sidel patented this unique technology – Sidel Predis™ – which uses hydrogen peroxide mist to sterilise the preforms.
Sensitive drinks can be affected by various factors when they are packaged – micro-organisms, light, oxygen and temperature. When Sidel’s scientific expertise on beverage packaging and industrial production is involved early in a new product packaging project, producers are able to optimise bottle performance while ensuring product safety and quality.
The end result is reliable, simple and safe aseptic beverage production in PET bottles, ideal for products distributed at ambient temperature. Additionally, it can help to lengthen shelf life and reformulate more sensitive beverages that would otherwise need added preservatives to maintain food safety.
How does Sidel’s packaging technology consider consumer perception, especially regarding the feel and taste of beverages? Are there any studies or feedback that guide your design decisions?
End user satisfaction drives the entire design and production process. At Sidel, we reproduce the consumer experience through sensory tests to ensure beverage quality, taste, and mouthfeel remain as desired.
Our bottles are stored in replica storage, as seen throughout the supply chain, and our dedicated sensory specialists conduct tests to ensure the beverage’s organoleptic characteristics remain unaltered.
Could you provide examples of how Sidel collaborates with beverage producers to tailor packaging solutions that maintain their products’ desired texture and mouthfeel?
We are able to support customers from an early stage in the development of new products, from concept to delivery. Our packaging experts will help define the best bottle shape, combining creative and technical skills to achieve a standout pack with the desired user experience.
Ferrarelle Società Benefit, one of the largest mineral water producers in Italy, partnered with Sidel to install its first aseptic line at its Boario plant to produce its product range of Vitasnella ‘Le Linfe’ functional water and teas. The installation of Sidel’s Aseptic Combi Predis was essential for ensuring a high-end taste experience, product integrity, and a long shelf life.
The company utilised its Predis™ dry preform decontamination solution—a safe, hygienic, and cost-effective way of packaging a variety of sensitive beverages.
As a result of this solution, Boario’s line can handle two different bottle formats, 0.5 litres and 1.25 litres, and can produce 18,000 bottles per hour. In addition to this efficient production process, the final consumer can satisfy their thirst with a high-quality tea beverage.
What advancements in sealing technology is Sidel implementing to ensure the integrity of beverages, particularly in preserving carbonation and preventing oxidation?
Sidel works closely with third parties that design sealing technologies to provide the best possible solution for each of our customers. For sensitive products, Sidel delivers a unique protocol of microbiological tightness to ensure product safety. This protocol is widely recognised and used by cap suppliers and beverage producers to validate their sealing design.
Looking towards the future, what trends or innovations in packaging does Sidel foresee as pivotal in further enhancing the preservation of beverage texture and mouthfeel?
There is no doubt that sustainability has been the driving force behind bottle design in recent years, not least because of new packaging regulations such as the Packaging and Packaging Waste Regulation and Single-Use Plastic (SUP) Directive, which have had a huge impact on the sustainability practices of the packaging manufacturing industry.
At Sidel, we’ve introduced specific solutions to help beverage manufacturers reach their sustainability goals. For example, our bottle lightweighting expertise has supported the dairy market in reducing bottle weight by up to 29.4 per cent (for 1L bottle in EU going from 35g to 24g), and our advanced blow moulding process has enabled the use of rPET resin. Innovative mould technologies and dedicated bottle design has assisted manufacturers in utilising a high-end bottle made from 100 per cent rPET, and our experts have also supported producers to embrace returnable PET and glass.
Pioneering the Future of Textural Excellence in Beverages
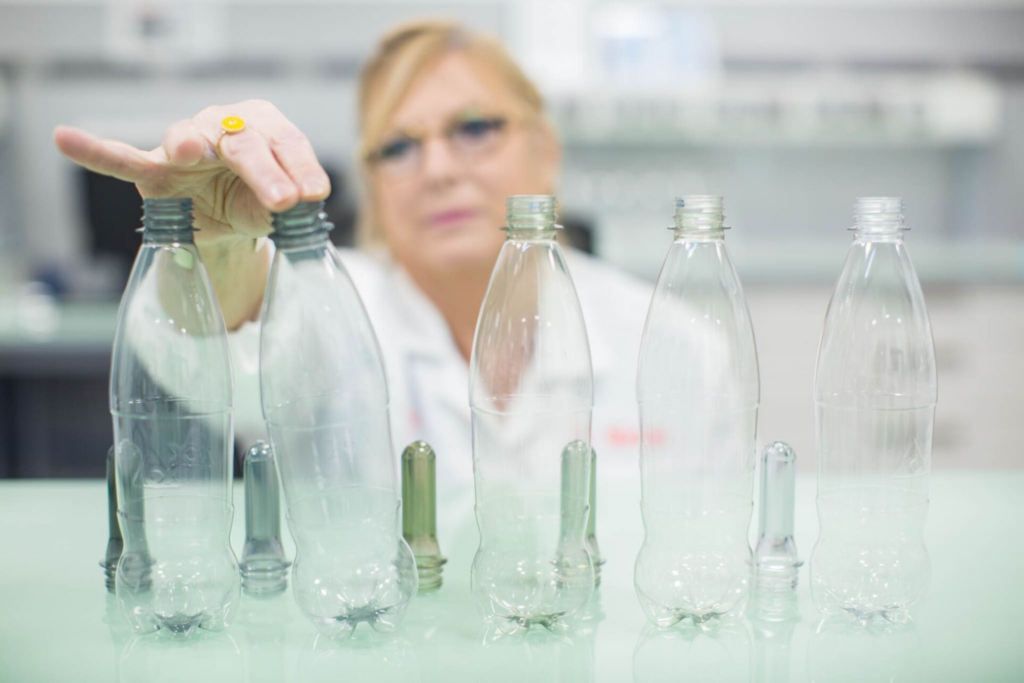
As the dialogue with Naima Boutroy unfolds, it becomes evident that Sidel’s commitment transcends mere preservation; it’s about enriching the beverage journey with an impeccable focus on texture and mouthfeel.
This innovative approach signifies a shift in the industry’s narrative, highlighting sensory dimensions’ importance beyond flavor. Sidel’s technological prowess and forward-thinking strategies herald a new era where every sip of a beverage is a harmonious blend of quality, sustainability, and sensory delight.
By championing the cause of texture and mouthfeel, Sidel is redefining packaging norms and setting the stage for a future where beverages are celebrated for their comprehensive sensory profiles, offering consumers an experience that truly resonates with the essence of the drink.