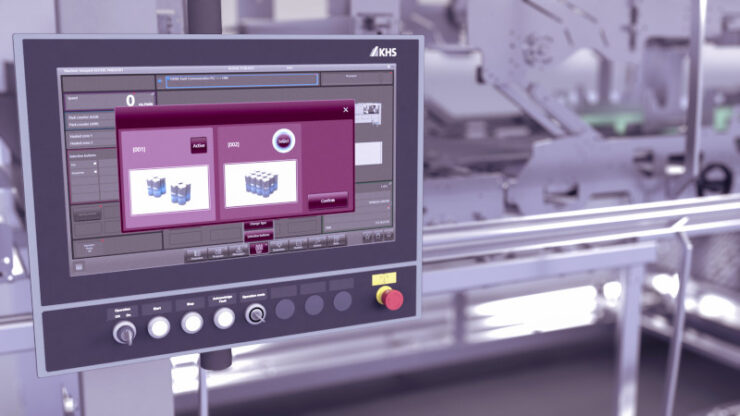
Courtesy of Jan Schwerdtfeger/KHS
- Automation of process modules on packing systems and palletizers
- Up to 30 minutes saved per format changeover
- Improved reproducibility and easier operation
More efficiency, speed, and reliability in the beverage can packaging process: KHS has automated the product infeed and formatting on its packing systems in the Innopack Advanced series and Innopal PB palletizers with robot grouping. This makes the switch to new products much faster and simpler than processes involving manual format changeovers. Up to 30 minutes can therefore be saved per format conversion. At the same time, a constant setting accuracy during changeovers increases the degree of reproducibility.
With the beverage industry undergoing dynamic development, the demands made of bottlers regarding fast reaction times in the adaptation of primary and secondary packaging are increasing. At the same time, with extended setting options available, the complexity of packaging machines is also growing, as is the use of format parts. “We’re meeting these challenges with an automation concept that not only reduces the time and effort needed for machine conversions to other products or packaging styles but also makes them more reliable and efficient,” says KHS product manager Ernst van Wickeren.
Greater efficiency on KHS packers
Partly automated format changeovers can be easily implemented on practically all packaging systems in the Innopack Advanced series. During the development thereof, the experts at KHS initially concentrated on the product infeed and formatting process modules that usually involve a relatively high amount of conversion work for the operator. For instance, at the machine infeed the containers are fed to the packaging segment through lanes with railings. When a new format is to be run, the user has to release and adapt between 30 and 50 adjustment points on the lane railings depending on the can diameter. With the partly automated format changeover concept, this is done at the press of a button, meaning that all that remains to be done is to ensure that there are no containers in the infeed during the changeover.
Furthermore, the adjustment units are now motorized and operated automatically. According to van Wickeren, the maximum degree of automation on KHS packaging machines has by no means been reached. “There are still format change parts that require manual replacement. We’re thus working tirelessly to find further solutions here.”
Full automation during palletizing
On the Innopal PB palletizer with robot grouping KHS has already fully automated format changeovers. “These are now performed at the press of a button, likewise with complex formats,” explains Christoph Wiesenack, palletizing product manager at KHS. “In addition to the automated systems already available, the centering systems on all variants in the Innopal PB series can be equipped with servomotors with immediate effect.”
This saves time during conversion and enables the grouped packs to be collated and placed on the pallet with the utmost precision. As clamping jaw changeovers on the grouping robots, pusher width adjustment, and guide adjustment are now all automated, no more manual intervention is needed on the palletizing machine. This increases operational safety.
Improved reproducibility
The improvements made in the packaging and palletizing section and the reduced complexity of format changeovers lower the demands made of operators and the number of employees required in general. At the same time, KHS reduces the error rate, for instance, owing to discrepancies in settings caused by shift changes at the bottling plant. “The motors always run to the exact set position automatically, therefore considerably improving reproducibility,” van Wickeren states. No subsequent adjustment is necessary, meaning that production can resume at full capacity immediately following a changeover. In total, the maximum time saved by automation amounts to 30 minutes per format changeover on packaging systems and 20 minutes on palletizers.