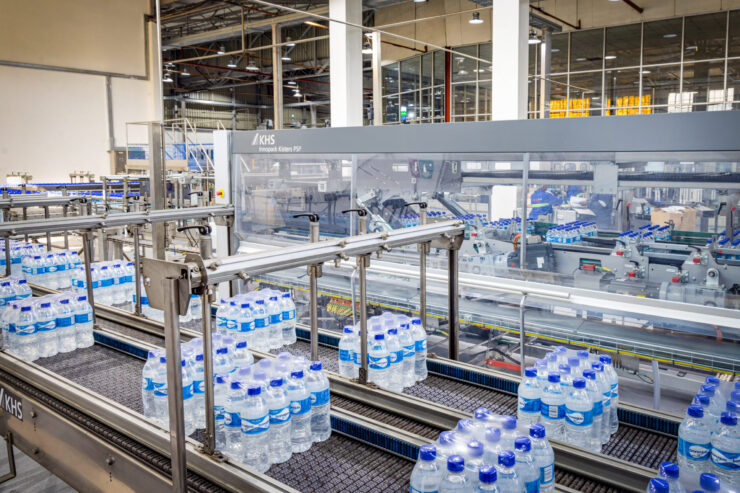
Courtesy of KHS
A big step towards cutting greenhouse gas emissions: now that KHS has installed an ultramodern non-returnable PET line for Schweppes Zimbabwe Limited (SZL), the bottler’s production setup is not only much more efficient but also saves on resources – at an increase in capacity of 300 per cent compared to the replaced production line.
Until very recently, the production shop at Schweppes Zimbabwe Limited in the Willowvale industrial area in the capital of Harare called for low-volume outputs.
The recent installation and commissioning of a completely new non-returnable PET line had the beverage producer convinced; it is equipped, among other things, with a compact InnoPET BloFill stretch blow moulder/filler block for the manufacture and filling of up to 36,000 containers per hour, the efficient Innoket Neo labeller for roll-fed labelling of the bottles, the Innopack PSP Advanced shrink packer and the flexible Innopal PB N palletiser. Continuous monitoring by KHS inspection technology ensures that only containers of perfect quality leave the plant. There were many reasons behind the decision to award the Dortmund turnkey supplier the contract, as Ms Ropafadzo Gwanetsa, corporate affairs executive at Schweppes Zimbabwe Limited, explains. “KHS is considered to be a reliable systems provider by our parent company, The Coca-Cola Company, and is valued for its expertise in highly efficient filling and packaging systems. Its range of holistic services that includes extensive technical support is also convincing.”
Production capacities increased by 300%
SZL continues to be extremely enthusiastic about the speed of the line in particular; compared to the previous competitor setup, Gwanetsa reckons that production capacity has increased by 300% – so much so, in fact, that the company’s current warehouse will probably have to be enlarged. This was a necessary step to take, for the demand for filled juice from flagship brands Mazoe Orange Crush or Minute Maid and for Bonaqua and Schweppes still water continues to grow on the domestic and regional markets.
Production is also proving more professional than before in its flexible processing of various packaging formats, holding between 400 millilitres and two litres. “The ability to easily process a whole range of different container sizes on a single line, with format changeovers now much quicker, gives us a great competitive edge over other bottlers,” says Gwanetsa, who also appreciates the automated processes on the new acquisition. “Operator intervention on the line has been reduced to a minimum, thus improving the efficiency of our production line.”
Gwanetsa illustrates the positive development brought about by modernisation with further figures. “We’ve managed to cut our overall costs by about 80 per cent compared to the former setup, with a 10% reduction in personnel requirements making a positive contribution to this.” Regarding resource savings, the new KHS plant engineering also scores with an up to 30 percent decrease in energy consumption, savings in water and CO2 and similarly reduced labelling costs. “Together with the entire group, we’re adopting an ambitious sustainability strategy with a directly noticeable cut in greenhouse gas emissions and also aiming for climate neutrality. Our state-of-the-art KHS technology is helping us to successfully pursue this objective.”
Less plastic use thanks to lightweighting
Savings in resources are also being made by the consumption of less material for primary packaging. Thanks to proven KHS stretch blow moulding technology, high-quality lightweight PET containers are now manufactured using up to 10 to 15 per cent less raw material.
Gwanetsa mentions a further major criterion with respect to sustainability: the long service life of the machines. “We’re factoring in the new NRET PET line for the next 20 years,” says the Schweppes expert. The longer the bottler operates a line, the lower its ecological footprint throughout its entire life cycle. “Our machines are often in successful operation for customers over several decades, with this alone meaning less impact on the environment,” confirms Bradley Naicker, KHS sales manager for South Africa, who reports on one special challenge faced in the course of this particular project.
As the amount of room available at the Schweppes production site in Harare was extremely limited, and the new system had to be installed in a small area, the KHS experts adapted the machinery to fit the available space. The line was thus installed in an L shape instead of the usual rectangle – in record time. Just six weeks after installation, the first saleable product ran off the belt – thanks to the excellent cooperation between KHS’ and SZL’s project teams.
Customer’s individual palletising requests met through advanced innovation
Special customer requirements also needed to be met in the robot palletising section. As the PET bottles are produced in certain special formats, the bottler uses specific pallets that, like the containers, do not correspond to the norm. “We were able to adapt the robot palletiser to pack the respective SKUs through individual robot programming and thus achieve an optimum result,” Naicker explains. Schweppes’ utmost satisfaction was ultimately sealed by the systems supplier’s successful project processing performance. “Through KHS’ holistic range of services, we benefitted greatly from the close support provided for the entire duration. This was manifested in the training we were given and the global transfer of knowledge from KHS engineers to our local team. After commissioning, we’ll continue to receive further training remotely,” says Gwanetsa. “Processing times are short and the engineers are always available.”
KHS ReDiS (Remote Diagnostic Service) has proved to be a valuable system and has greatly supported the skills transfer process and maintenance of the line as commissioned.
Naicker happily looks back on what has been achieved here. “We’ve exceeded expectations regarding production capacities, economy and the use of resources. SZL is now bottling more beverages of a better quality at a lower cost and with a smaller carbon footprint.”