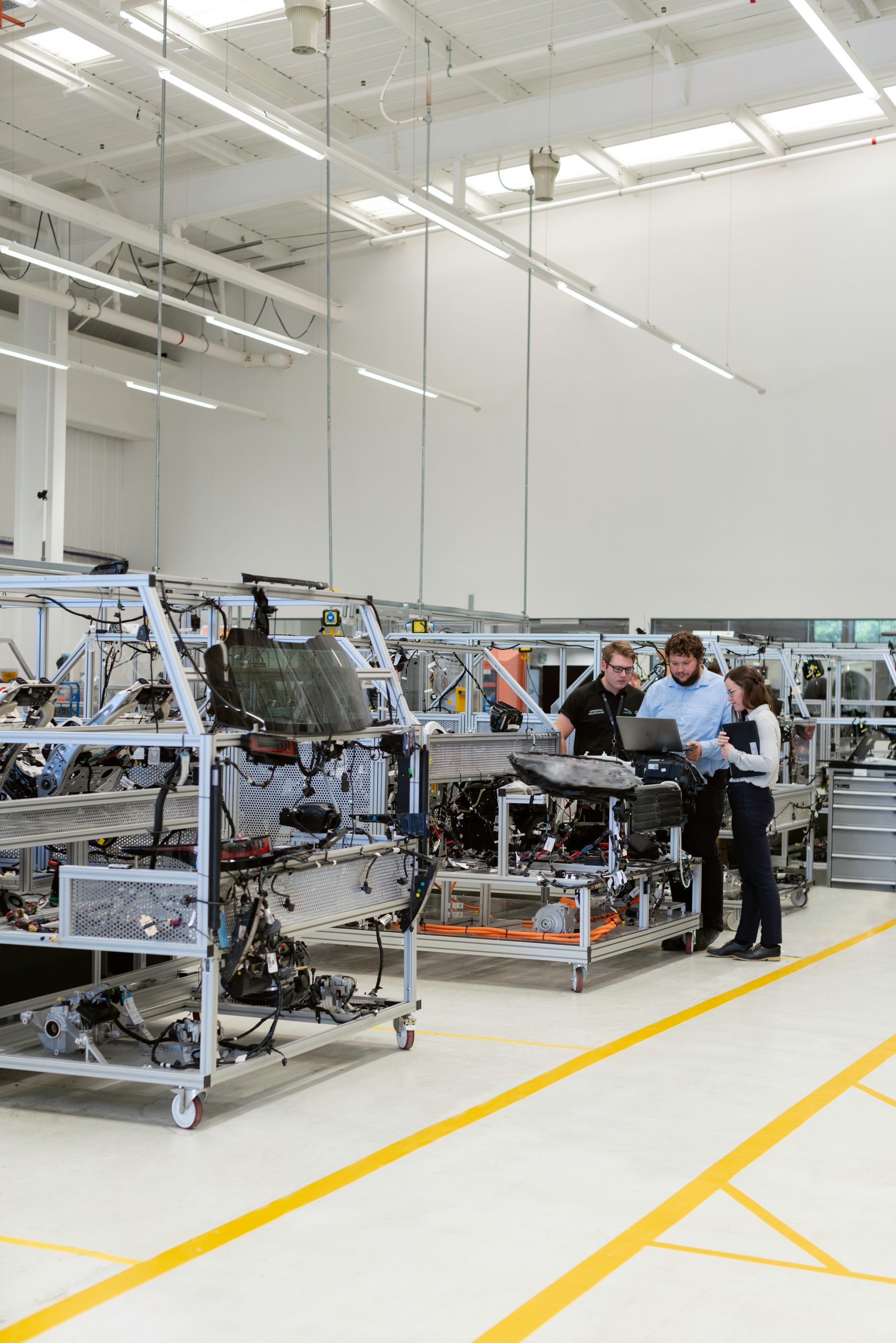
This is Engineering/Unsplash
The food and beverage industry is on the road towards digitalisation, with more companies adopting robots and automation solutions across their operations. There certainly has been some shifts from the automotive industry being the primary driver of robotic technologies, to these innovations reaching non-traditional segments like F&B. According to a study conducted by Meticulous Research, food robotics is expected to grow at a CAGR of 11.6% from 2021 to 2028, reaching a valuation of $2.08 billion by 2028.
Rising investments are also driven by governments offering lucrative support. For instance, in Singapore, eligible enterprises can receive up to SGD 10 million in investment allowance for this type of technology.
It’s looking to be a promising market outlook for automation, as the cost of adoption and ownership has gotten lower in the past few years. More players are stepping into the industry, engaging in different parts of the ecosystem, from manufacturing to distributing robotics solutions.
It’s essential for businesses to advance towards technology in this day and age, and the COVID-19 pandemic has propelled it even further in the F&B industry. Robotics have become a viable solution that addresses labor shortage issues that has been plaguing the segment recently. This technology allowed streamlining of processes and mass production in order to meet the demand of the increasing population.
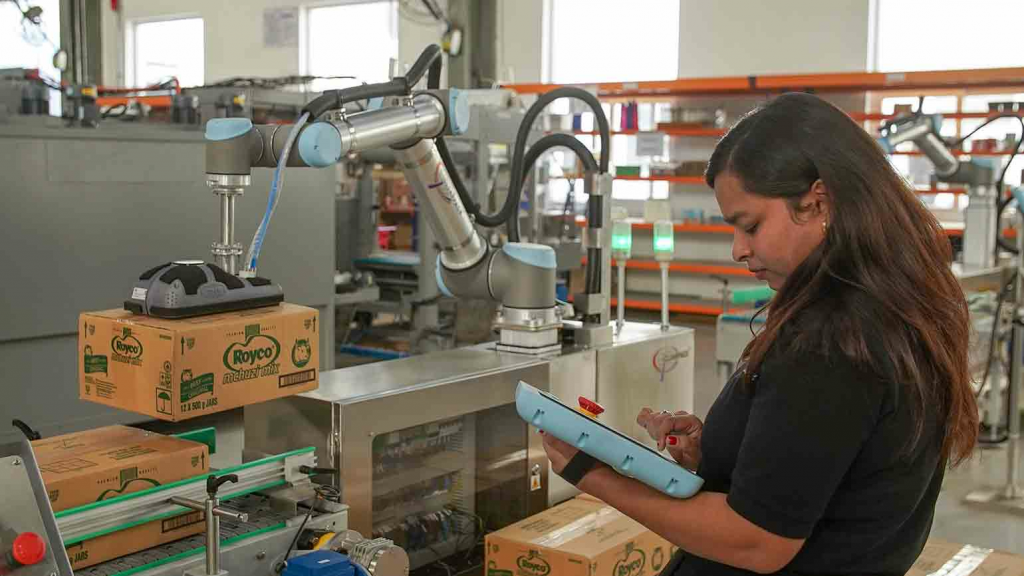
The natural way forward
The past decade has indeed been a testing time for companies looking to adopt automation solutions in their businesses. “The F&B industry, [in particular], is going through a transition period in order to satisfy the appetite of the next generation,” chimes Swami Vangal Ramamurthy, Division Head of the Robotics Business Division at OMRON Asia Pacific.
In particular, there is a shift towards mass customisation, which is automation’s sweet spot. Opportunity lies in being able to provide variety while still meeting the volumes necessary to cater to demand.
Solutions for F&B revolve around increased flexibility and configurability, keeping in mind top productivity and efficiency for quicker changeover, since there are more people buying packs for on-the-go or in-home dining. This also addresses the issues on food security, something that has been a concern in the past two years.
Robots are also being incorporated as part of a broader solution within a machine, moving from end-of-line applications like palletizing. These unified robots would then be controlled by a single PLC system, loading for packaging, cartooning and casepacking. Pick-and-place equipment and machines that combine traditional and advanced motions are increasing in adoption, as well.
More companies are also utilising robots that are involved in actual food production, machines that handle the raw materials or food product. The dedicated robots are constructed with hygiene and food safety in mind, while ensuring that the food is carefully handled during production. These come in IP65 or IP67 ratings, can withstand industrial cleaning and washing and may have UV disinfection systems integrated for maximum sanitation.
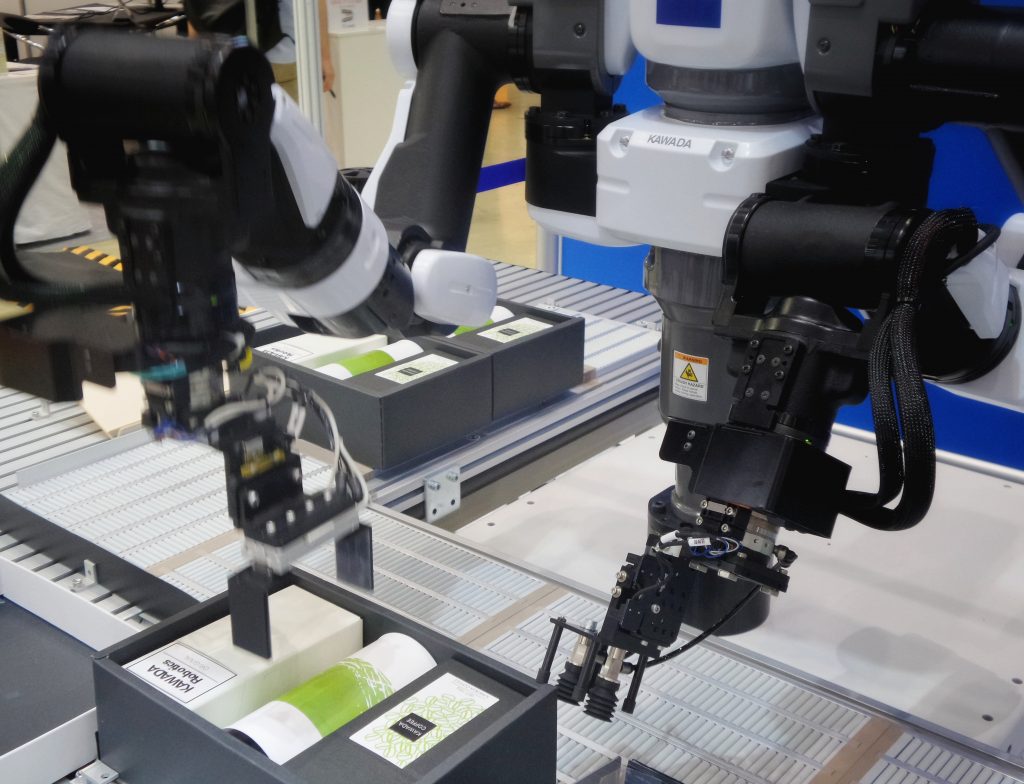
Collaborative and autonomous solutions
Despite the growth automation has seen in F&B, there still exists a misconception that robots will eventually replace the human workforce. In time, factories will be taken over by machines. However, this doesn’t seem to be the reality. In fact, robots have made the lives of operators and the workforce easier by taking away menial, physical work, and freeing up time to focus on more high-level tasks. According to a World Economic Study, robotics has the potential of creating 58 million jobs globally in the next five years.
Rather than elimination, a human-machine collaboration is taking place, with robots working alongside people in tasks. Collaborative robots, ‘cobots’, are a minimally invasive solution that has become a game-changer in a number of companies. Universal Robots is one that has provided a range of solutions, from cobots that can replace traditional shielding packaging machines, to those that can automate the analysis of raw material samples.
Cobots can be incorporated in environments with special climate and hygiene requirements, which may be dangerous for a person to be in. These can perform complex processes in low oxygen conditions, while making sure that food standards are met. For F&B specifically, these are completely sealed to avoid dust and other particles from contaminating the item.
Safety of the human workers on the shop floor is also improved once robots are integrated as they can perform injury-prone and dangerous parts of manufacturing. For cobots, in particular, workplace injuries are reduced by 72% as they can be modified to include their own safety features like automatically stopping or pausing. Program safety boundaries and parameters can be adjusted once the industrial robot is deployed.
Artificial intelligence (AI) is another key component in robotics solutions adopted for F&B. These autonomous robots can collect and process a number of parameters simultaneously, which are great as vision, inspection and traceability systems. “They are able to monitor the assets and provide support proactively, thus ushering a new era in manufacturing,” according to Steve Mulder, Regional Industry Manager at Rockwell Automation.
The supply chain will be filled with reliable and robust systems, with different segments of the food production connected for maximum efficiency. Real-time data is key to making these solutions work, as operators can easily adjust parameters when needed. It can make predictability a possibility as companies can determine when machines will need maintenance
Automation and robotics solutions are ideal for the F&B industry, that thrives in zero-defect processing and careful handling. As these are introduced in wider landscape, it’s necessary for businesses to undergo the necessary education and training to ensure they maximise the benefit these innovations bring.