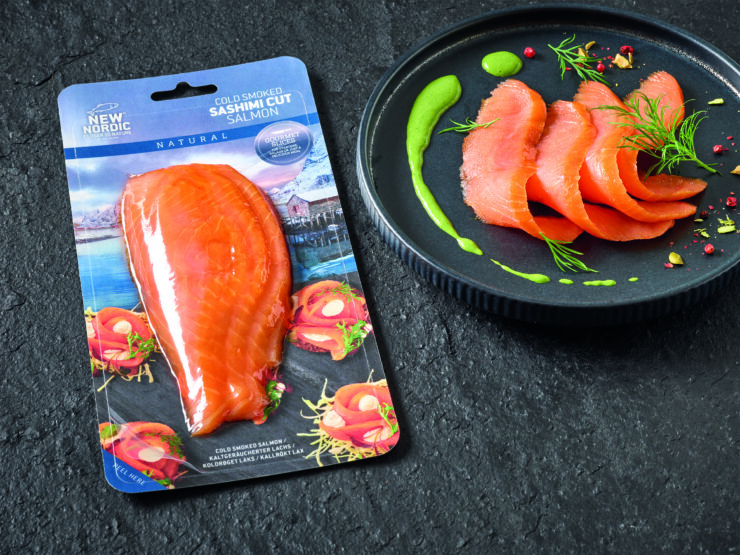
Courtesy of SEALPAC
SEALPAC’s Amax traysealers: versatile in applications and materials, consistent in performance and efficiency
When it comes to the SEALPAC Amax-series traysealers, the name says it all. Based on decades of experience in tray-sealing, they have been designed to achieve previously unattainable, maximized results in terms of productivity and efficiency. These machines are characterized by their economical use of energy and particularly low-wear design. This reduces maintenance costs and increases their availability in the production area.
Each Amax traysealer reliably processes a wide variety of trays and film, including today’s resource-saving combinations.
Maximum performance, flexible in use
Our latest generation of SEALPAC traysealers, the Amax-series, sets new standards in performance. Subject to the application, these state-of-the-art machines achieve up to 50 percent higher outputs. Depending on the selected model (A4max to A10max), they will seal up to 196 trays per minute under a modified atmosphere.
Next to traditional MAP and TraySkin® packaging, these flexible traysealers can handle particularly innovative packaging solutions that stand for more resource conservation. For example, they process ultra-light trays, the weight of which has been reduced by 20 percent compared to conventional MAP trays. Hybrid packaging concepts with a reduced plastic and high cardboard content, such as eTray®, FlatSkin®, or FlatMap®, can also be handled by the SEALPAC Amax traysealers. At request, we offer you an all-in-one solution, which allows you to run all these concepts on the same base machine.
Focus on sustainability, also in machine construction!
In times of high energy costs and rising raw material prices, the Amax-series offers a highly efficient operation. Next to their economical consumption of materials, they are characterized by their particularly compact and, at the same time, low-wear, low-maintenance design. SEALPAC Amax-series traysealers are driven by reliable servo motors, which ensure the smoothest production runs. The integrated EnergyManager adjusts the line speed to the actual tray feed, to keep energy consumption as low as necessary. By using servo technology, the air consumption of the Amax traysealers was reduced by up to 90 percent. However, SEALPAC not only stands for more sustainability in terms of energy use but also allows the existing tools of the SEALPAC A-series to be used on the new Amax-series traysealers. This saves production costs and space.
Smart features, for digitized production environments
The high-tech Amax traysealers are tailored to the needs of Industry 4.0. and offer all the necessary prerequisites for comprehensive digitization of industrial production. The operating data are available in real-time and accessible from any location via an internet connection. Furthermore, each model within the Amax-series is equipped with the innovative iMode control. It manages the speed of the entire process according to a simple principle: the number of packages to be sealed per minute, as specified by the operator. This determines the speed of all subsequent processes. The result is an increasingly optimal packaging process, which, if necessary, extends to the maximum physical limits set by the product and the packaging materials.
When it comes to the SEALPAC Amax-series traysealers, the name says it all. Based on decades of experience in tray-sealing, they have been designed to achieve previously unattainable, maximized results in terms of productivity and efficiency. These machines are characterized by their economical use of energy and particularly low-wear design. This reduces maintenance costs and increases their availability in the production area.
Each Amax traysealer reliably processes various trays and film, including today’s resource-saving combinations.
Maximum performance, flexible in use
Our latest generation of SEALPAC traysealers, the Amax-series, sets new standards in performance. Subject to the application, these state-of-the-art machines achieve up to 50 percent higher outputs. Depending on the selected model (A4max to A10max), they will seal up to 196 trays per minute under a modified atmosphere.
Next to traditional MAP and TraySkin® packaging, these flexible traysealers can handle particularly innovative packaging solutions that stand for more resource conservation. For example, they process ultra-light trays, the weight of which has been reduced by 20 percent compared to conventional MAP trays. Hybrid packaging concepts with a reduced plastic and high cardboard content, such as eTray®, FlatSkin®, or FlatMap®, can also be handled by the SEALPAC Amax traysealers. At request, we offer you an all-in-one solution, which allows you to run all these concepts on the same base machine.
Focus on sustainability, also in machine construction!
In times of high energy costs and rising raw material prices, the Amax-series offers a highly efficient operation. Next to their economical consumption of materials, they are characterized by their particularly compact and, at the same time, low-wear, low-maintenance design. SEALPAC Amax-series traysealers are driven by reliable servo motors, which ensure the smoothest production runs. The integrated EnergyManager adjusts the line speed to the actual tray feed to keep energy consumption as low as necessary. By using servo technology, the air consumption of the Amax traysealers was reduced by up to 90 percent. However, SEALPAC not only stands for more sustainability in terms of energy use but also allows the existing tools of the SEALPAC A-series to be used on the new Amax-series traysealers. This saves production costs and space.
Smart features, for digitized production environments
The high-tech Amax traysealers are tailored to the needs of Industry 4.0. and offer all the necessary prerequisites for comprehensive digitization of industrial production. The operating data are available in real-time and accessible from any location via an internet connection. Furthermore, each model within the Amax-series is equipped with the innovative iMode control. It manages the speed of the entire process according to a simple principle: the number of packages to be sealed per minute, as specified by the operator. This determines the speed of all subsequent processes. The result is an increasingly optimal packaging process, which, if necessary, extends to the maximum physical limits set by the product and the packaging materials.