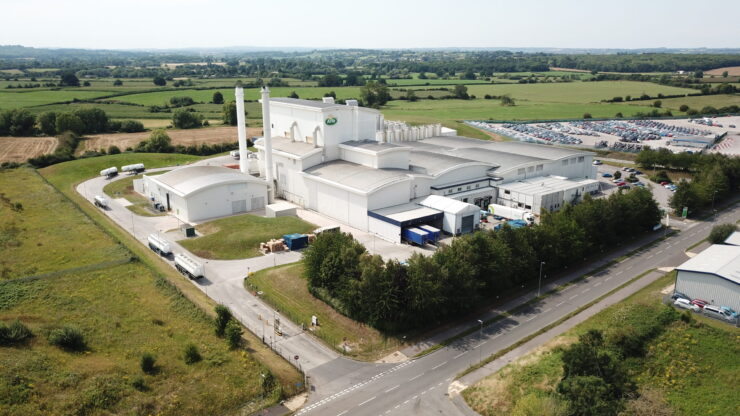
Courtesy of Grundfos
By Cath Isabedra
The food and beverage (F&B) industry significantly impacts the environment due to its resource-intensive production processes. In particular, water and energy consumption are two critical areas where F&B manufacturers can dramatically impact their sustainability targets.
Water scarcity is a growing global concern, with 1 in 3 people experiencing water scarcity and 1 in 9 lacking access to clean water1. The F&B industry significantly contributes to water usage, with approximately 70 percent of global freshwater withdrawals going toward food production2. However, by implementing water-efficient solutions, such as water recycling, conservation measures, and innovative technologies, F&B manufacturers can reduce water consumption and achieve sustainability goals. For instance, by using closed-loop water systems, F&B manufacturers can recycle wastewater for non-potable uses, such as cleaning, irrigation, and cooling, reducing their overall water usage3.
Similarly, energy usage is another critical area where F&B manufacturers can improve their sustainability practices. According to the International Energy Agency (IEA), the F&B industry is responsible for approximately 7 percent of global energy consumption4. However, by implementing energy-efficient solutions, such as energy-efficient lighting, process optimization, and renewable energy sources, F&B manufacturers can significantly reduce their carbon footprint and energy costs. For instance, using renewable energy sources, such as solar or wind power, can help F&B manufacturers transition to cleaner energy sources and reduce their greenhouse gas emissions5.
Grundfos, a global leader in advanced pump solutions and water technology, has taken several initiatives toward water and energy efficiency. The company’s focus on sustainability is reflected in its mission to be a responsible and sustainable company that contributes to developing a better world.
Eric Lai, Regional Managing Director for Grundfos’ Industry Performance Unit for the Asia Pacific region, and Country Director for Singapore, shared his insights into how their company is answering the calls for sustainability.
For manufacturers, what else can they look at – beyond sustainable ingredient innovation – to reduce the impacts of climate change?
The food sector is responsible for about 30 percent of global energy consumption6 and more than one-third of global greenhouse gas emissions7. With food production processes as the leading contributor to overall food system emissions – representing 39 percent of the total – food manufacturers and processors play a critical role in the shift towards decarbonisation.
Thus, it is important for F&B manufacturers to weave sustainable solutions across all their manufacturing activities. Given the prevalence of pump and pump systems and their critical role across major utility and process systems at any F&B plant, they hold great potential in helping F&B manufacturers improve energy efficiency, lowering their carbon footprint.
What are the most critical components of a successful sustainable manufacturing strategy?
It is crucial for F&B manufacturers seeking to advance their sustainability journey to gain an understanding of their current environmental performance, including evaluating factors such as energy and water consumption and emissions generated from manufacturing processes. This will provide the opportunity to identify areas that require the most improvement, where the most impact can be made, and the processes and products in which more sustainable practices can be integrated.
A clear understanding of these priority areas enables manufacturers to establish goals and timelines for their sustainable manufacturing journey before determining the suitable actions for implementation.
An example of how we are helping F&B manufacturers seeking to reduce their carbon footprint is through conducting energy checks. Grundfos’ Energy Check Advanced uses actual pump data in terms of flow, head, and motor power consumption along with pump age and operating hour, giving manufacturers an overview of the life-cycle costs (LCC) of one or more pumps. This, in turn, helps facilitate crucial decisions on pump replacement and cutting energy consumption, benefiting their financials and the environment.
Are there any innovative approaches that food manufacturers have utilised to operate sustainably?
Technological innovation has and will continue to play a big role in advancing sustainability in food manufacturing. However, what F&B manufacturers should not overlook is collaborating with key partners across their value chains to optimise their operations.
For example, Arla Foods, one of the leading players in the international dairy market, is tapping into the expertise of its network of suppliers and partners to bolster sustainability across their operations. Arla has kicked off their journey towards a 2050 target of carbon net zero emissions, starting with the aim of lowering carbon emissions by 63 percent at 60 dairies worldwide by 2030, and Grundfos plays an essential part in these plans.
In 2022, Grundfos was appointed to identify, report, and achieve energy reductions across Arla’s global dairy sites, helping to enhance core systems by replacing pumping systems with high-efficiency systems with state-of-the-art motors, pumps, and controls.
At present, we have assessed two-thirds of Arla Foods’ sites and have identified annual savings of seven gigawatt-hours, with total expected savings of around ten gigawatt-hours.
As part of this project, we have replaced the old pumps with our new intelligent pumps for chilled and iced water applications at Arla Westbury dairy in the UK, leading to savings per year of 481,800 kWh energy and 194 tons CO2, with a return on investment of less than two years.
How do you measure the success of your sustainable operation efforts?
The best way to assess success is to measure the results against the goals set at the beginning of any project. For Grundfos, we work with key metrics most important to our partners as we provide customised solutions catering to their specific goals. In general, savings in energy and water, reuse of water, and wastage reduction are some of the most common metrics to measure the success of any sustainable operation effort.
Specifically for pumps, F&B manufacturers need to think about system efficiency and take a longer-term view when evaluating products and solutions. It is estimated that 85 percent of the LCC of a pump can be attributed to its energy costs. That’s why it is critical to size pumps correctly and focus on the energy efficiency metric. In a typical life cycle of 10 – 20 years of a pump, a small difference in energy efficiency can lead to huge differences in energy consumption and carbon emissions.
What are the current challenges the food industry faces when it comes to delivering and operating sustainably?
Megatrends, such as climate change, the growing global population, rising food insecurity, and water scarcity, are driving up pressure on food manufacturers to operate more sustainably. This is especially true in South and Southeast Asia, which constitutes the region with the greatest food production-related emissions, producing 23 percent of the global total8.
To keep pace with greater calls for sustainability, the food industry must overcome barriers to adopting newer, intelligent technology to make manufacturing processes more efficient and sustainable. A major barrier is the cost, including upfront implementation and maintenance costs. Companies need to realise that while advanced intelligent technology can cost more upfront, the benefits, in the long run, will exceed the upfront investment.
Additionally, the cost will be less of a barrier once such innovations are met with greater demand and are further developed on a larger scale. This is why it is crucial for businesses to actively embrace new innovations. When new sustainable solutions see greater demand from manufacturers, solution providers will subsequently achieve greater economies of scale as they increase production and lower costs.
What does the future look like in terms of sustainable food manufacturing? How can food manufacturers be a step closer to fully achieving sustainability?
Moving forward, we believe the drive to sustainable food manufacturing will continue to accelerate in line with the adoption of circular models of operation. Embedding circular principles throughout their business will enable manufacturers to design waste out of the resource ecosystem and maximise the value of resources by keeping them in use for as long as possible.
We need to keep in mind that food production is both highly water and energy-intensive, as water is used at each step across the value chain, and energy is consumed to move them throughout the process. For manufacturers to achieve the best outcome for water and energy consumption, they must first consider the water-energy nexus. To harness water and energy resources as sustainably as possible, manufacturers should leverage holistic, long-term solutions that build efficiency into integrated systems, aiming to do more with less.
An example of how circularity has been successfully embedded in the operations of F&B manufacturers is our work with Carlsberg. Together with other partners, Grundfos supported the development of a Total Water Management (TWM) treatment plant at Carlsberg’s production facility in Fredericia, Denmark, which allows the plant to recover and reuse 90 percent of its process water. The TWM model is critical to Carlsberg’s ambition to reduce water use in its breweries by 50 percent by 2030.
Any additional insights you’d like to share about how Grundfos is working to make sustainability happen?
Sustainability is a crucial part of Grundfos’ DNA. We recently became the first organisation in the water solutions sector to receive full validation of our 2050 net-zero target from the Science-Based Targets initiative (SBTi), a climate action organisation that enables companies to set greenhouse gas (GHG) emissions reduction targets grounded in science. SBTi also validated Grundfos’ near-term 2030 emission reduction targets.
In the process of developing our net-zero target and roadmap, we worked with industry experts to identify the GHG emissions across our value chain and found that 99 percent of our total GHG emissions came from the use of our products by end users. That reaffirmed our belief that we can make the most difference in addressing the growing climate challenges by delivering the world’s most energy-efficient and digitally enabled product portfolio.
This is also aligned with our rationale for setting up a specialised F&B team in 2021. We want to get closer to our F&B customers and work hand-in-hand with them to better understand the gaps and opportunities in their sustainability journey. Ultimately, this allows us to come up with tailored solutions and services to help them achieve their ambitions and take their operations to the next level.
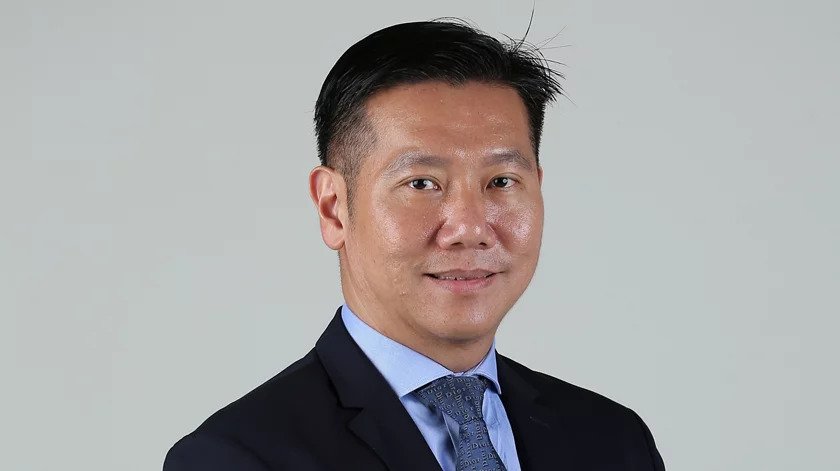
With insights from Eric Lai. Eric Lai is the Regional Managing Director for Grundfos’ Industry Performance Unit for the Asia Pacific region and Country Director for Singapore. In his role, Eric leads Grundfos’ sales and strategy activities relating to the industry market in the region.
Eric joined Grundfos in 2005, and rose through the ranks during the 16 years, holding several positions in APAC for product sales, APAC Industry segment, and as Global Machine Industry director. In 2020, he was relocated to China to lead the Industry business as Business Managing Director.
References:
- UN Water. (n.d.). Water Scarcity. Retrieved from https://www.unwater.org/water-facts/water-scarcity/
- World Wildlife Fund. (2019). Food and Water: An Inseparable Pair. Retrieved from https://www.worldwildlife.org/stories/food-and-water-an-inseparable-pair
- Environmental Defense Fund. (n.d.). Food and Agriculture: Water. Retrieved from https://www.edf.org/food-agriculture/water
- International Energy Agency. (2017). Energy Efficiency in the Food Industry. Retrieved from https://www.iea.org/reports/energy-efficiency-in-the-food-industry
- World Resources Institute. (2019). 3 Strategies to Reduce Your Carbon Footprint Through Renewable Energy. Retrieved from https://www.wri.org/blog/2019/02/3-strategies-reduce-your-carbon-footprint-through-renewable-energy
- Food and Agriculture Organization. (n.d.). Retrieved from https://www.fao.org/energy/home/en/
- UN News. Food systems account for over one-third of global greenhouse gas emissions. Retrieved from https://news.un.org/en/story/2021/03/1086822
- The Conversation. Xu, X. and Jian, A. (2021). Food production generates more than a third of manmade greenhouse gas emissions – a new framework tells us how much comes from crops, countries, and regions. Retrieved from https://theconversation.com/food-production-generates-more-than-a-third-of-manmade-greenhouse-gas-emissions-a-new-framework-tells-us-how-much-comes-from-crops-countries-and-regions-167623