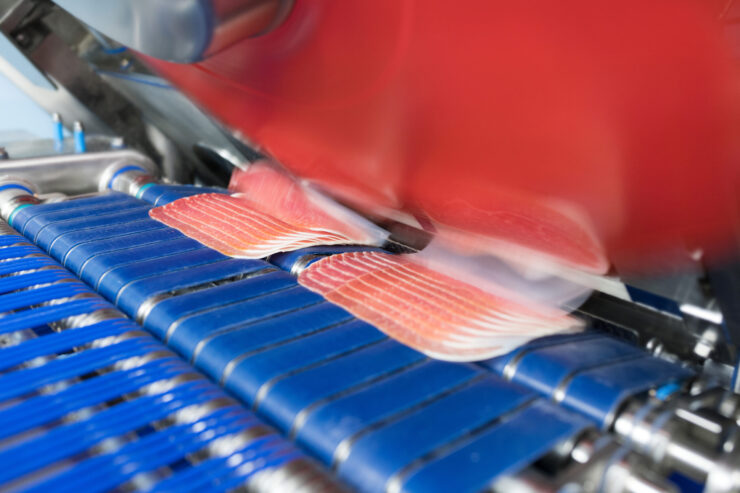
Courtesy of GEA
At this year’s IFFA, the world’s leading trade fair for meat processing, GEA will be presenting technological innovations for the One-Line-Concept for slicing and packaging food in Hall 8, Stand G10 in Frankfurt from 3 to 8 May. The new version of the line concept from GEA integrates new technology features and machines from pre-scanning meat, cheese, and alternative products to converging the slices, to help customers save raw materials (both product and packaging), increase production capacities, and improve sustainability.
Food manufacturers continually face new market challenges, including: the increasing need for more food and greater variety; increasing costs and price competition; an aging population with specific packaging needs; and the need to adhere to ever more onerous packaging and waste regulations. In practical terms, this means manufacturers must: focus constantly on minimizing their use of raw materials; reducing packaging volumes; improving recyclability of packaging, for example through the use of mono materials; increasing their production flexibility; and reducing energy consumption. GEA has addressed precisely these critical factors with its numerous technical innovations within its One-Line-Concept.
Advanced scanning and slicing
The One-Line-Concept brings together all relevant GEA technology and ensures that it is perfectly harmonized to work efficiently as a single production line. Within that, GEA has introduced a range of key advances that reflect the company’s focus on engineering excellence. The new OptiSlicer 7000 with single or dual drive allows simultaneous slicing of two natural products with the possibility to adjust each line to the target weight per pack. Depending on the product and application, the single drive can be used for high-volume production of calibrated products up to 2,000 kg/h, while the dual drive option allows for high yield and high-output processing of natural products. The machine is accessible from both sides.
The new R505 blade has a longer cutting edge that allows wider cuts with better portion control. These, combined with the new OptiScanner 5000, which scans the contours of the product before slicing to establish the optimum slice thickness and check the weight of the products. This reduces giveaway, improves throughput, and avoids unnecessary waste.
High savings through technological excellence
The impact of this efficiency is significant: in a specific application, reducing portion weight by just 2 grams in a 200-gram package could generate annual savings of 400,000 EUR for a two-shift operation.
Flexible and more efficient loading and packaging
GEA’s innovations continue further downstream in the production process. The GEA OptiLoader 6000 offers a new feature with the retract belt. This extra loading belt drops high stacks or multi-layer portions into the package with a retract of the belt, independently from the cycle of the GEA PowerPak. This option increases flexibility and improves process security.
The PowerPak 9000 thermoformer continues to hold its leading position in packaging with innovations in heating, evacuatio,n and gassing technologies (Modified Atmosphere Packaging) while providing greater automation, improved data collection, faster tool change and the greater opportunity to use mono materials for easier recycling without any compromise on pack quality or machine performance. The PowerLabel 7000 is a new modular labeling concept from GEA that represents leading technology for cross-web labelling. It provides top and bottom film labeling, fast changeover with improved accessibility (uniquely from just one side of the machine), and ensures high line Overall Equipment Effectiveness (OEE). At the end of the line, the PowerGuide 5000 converging system, which brings up to 6 lines into one, has benefited from continuous improvement for easier operation and higher performance.
Additionally, all GEA PLC-controlled machines are IoT-ready and seamlessly connected to the GEA Cloud, enabling smart data integration for real-time performance optimization.