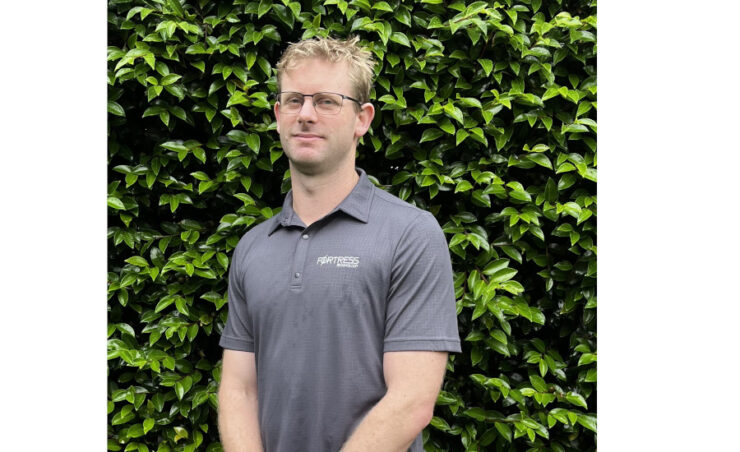
Courtesy of Fortress Terchnology
Former Manufacturing Manager of Dynamic Inspection Tim Whyte is confirmed as the new General Manager of Fortress Technology’s fourth global manufacturing hub in New Zealand.
Tim succeeds the founders of the firm, Bob Philpott and Steve Atkins, who are stepping down after growing the company into the market leader of food contaminant and checkweighing equipment in New Zealand, Australia, and neighboring APAC countries.
The appointment of Tim, who has worked for the New Zealand-based company for over a decade, ensures customers benefit from a well-rounded manager with the experience needed to support Fortress Technology’s next era of growth and maturity locally and globally. “This is an important growth stage for the company. I am humbled to lead Fortress Technology New Zealand at such an exciting time,” says Tim.
Making the food industry safer attracted Tim into the industry. Spending the past decade running the New Zealand manufacturing department and overseeing the service team, the electrical engineering apprentice previously worked as an electrician before completing further studies to qualify as an electrical inspector.
Tim joined the food safety specialist in 2013. He recounts that it has been an extensive yet rewarding learning experience that he anticipates will continue to provide new and interesting challenges. “The concept of fine tuning equipment to make the food industry even safer remains a huge draw personally and professionally. Having equipment familiarity is a real asset for leaders as it enables us to better understand and react to unique production challenges,” reports Tim.
Seamless Transition
Tim’s appointment was confirmed during a visit to Fortress Technology’s Toronto HQ. Seeing such close alignment in business values instilled further confidence that Dynamic’s longstanding legacy would be upheld and pave the way for greater food security and safety.
“There has been a collective sigh of relief from food processors and engineers across New Zealand that the face of inspection equipment for 25+ years – Bob and Steve – is seamlessly transitioning to a quality equipment brand they know and trust. This is a new and exciting chapter. New Zealand may be small, yet there’s extensive and untapped market potential underpinned by innovation and high yields,” affirms the company’s new General Manager.
Opening up the Fortress R&D department is already resulting in the emergence of new technologies to support evolving food safety requirements in the Tasman market. This, emphasizes Tim, is going to equip specific industries with market-defining QA, testing, X-Ray, Combination, and Checkweighing equipment.
Additionally, having closer proximity to the Australian market will enable Fortress to provide a more responsive service to local agents, which will help them grow, too. Having led the manufacturing team, Tim appreciates the drive and experience customers seek to accelerate their food safety strategies. He expands: “Fortress is uniquely positioned to customize production lines and respond rapidly to deliver food safety solutions that fit their evolving needs. Customers rightly expect the highest attention to detail and access to innovative new machinery to meet their evolving needs.”
With some remarkable pieces of technology in the pipeline, Tim is quick to assure New Zealand, Australian, and APAC customers that upholding standards remains his staunch focus.
“First and foremost, our priority is to serve our customers and keep food production lines running. However, having access to this bigger equipment portfolio, and much larger design and R&D talent pool, now means we can meet any site-specific inspection requirement. In turn, helping processors to expand their domestic and export market reach with assurance that they are complying to GFSI production standards.”
Fortress Technology produces customized inspection equipment with superior product design and engineering. Our product lineup includes Metal Detectors, Checkweighers, and Combination Systems designed with a Never Obsolete Commitment. We offer exceptional customer support, parts, software upgrades, and a global service team available throughout the product’s lifecycle. We prioritize customer needs and offer a full refund if products fail to perform as anticipated, demonstrating our confidence in our work. Our commitment to manufacturing high-quality equipment ensures customers’ needs are met efficiently and effectively.