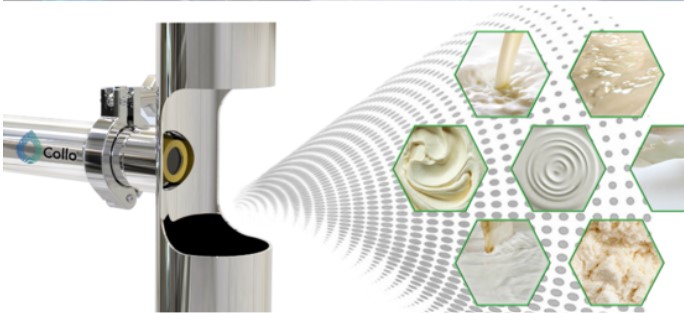
Courtesy of ColloidTek
Rising costs from inflation and increased focus on reducing carbon dioxide emissions make product loss management more critical than ever in dairy plants. These losses occur because timings or other process parameters are set incorrectly, causing many valuable dairy products to be unnecessarily washed with the wastewater. Collo’s unique liquid fingerprint technology addresses this problem by detecting any type of liquid in the pipes in real time, offering an easy way to optimise production and cut product losses.
The rising costs of raw milk, electricity, and other expenses drive dairy plants to focus more on reducing milk loss. The cost of raw milk has risen by 64 percent in two years in the EU region and, in some countries, significantly more.
With thin profit margins, it is a strategic imperative for many plants to minimise product loss. At the same time, there is global pressure to reduce the CO2 footprint of dairy production, and here milk loss at the plant plays a key role.
The scale of the problem is huge. Considering that the EU alone had more than 12.000 milk processing and production sites handling over 161 million tons of raw milk in 2021, significant volumes of milk could be saved, translating into greatly reduced carbon footprints for dairies across the EU by prioritising reductions in production losses.
“But to be able to minimise wasting valuable milk products, it is essential to know where in the process the leak happens,” says Mikko Tielinen, Head of Sales at ColloidTek. “With conventional methods, it is hard to meet that goal, which often results in milk products being unnecessarily flushed out with the wastewater. When a leakage then shows in the form of excess organic waste in the effluent, it is extremely difficult to determine where it is coming from.”
Millions of euros down the drain
For a typical dairy plant with an intake of around 250 million litres of milk per year, a loss of just 1 percent of the raw material corresponds to literally throwing about one million euros down the drain.
Tielinen points out that current solutions are insufficient for addressing the problem. Flow rate timing is inaccurate, and traditional sensors are unreliable and imprecise, with fouling and creep being significant issues. Several traditional sensors are necessary to detect different types of liquids, such as whey, cream, and cleaning chemicals, so the optimisation systems become complicated and expensive to manage.
“Our solution, on the other hand, offers an easy and very accurate way to detect where exactly in the process the leakage is,” Tielinen says. “It measures the exact real-time liquid fingerprint at any desired point in the process with a single EMF-sensor. Combined with machine learning, our solution ensures that the process stays optimised and easily monitored through our cloud solution.”
Addresses problems at the source
Usually, product losses in the process are noticed when there is an excess of organic material in the effluent. This can also be a sign of problems in production. However, measuring just the effluent does not tell why and where too much milk product is flushed out with the wastewater.
“As our technology can supervise all the draining points in real-time, it can keep track of the liquids in the pipes and show exactly where the leakage is,” Tielinen says. “This makes it possible to address the problem at the point of origin, saving huge amounts of milk and money.”
In addition to directly improving the profitability of a dairy plant, reducing milk waste also lowers the cost of wastewater treatment and helps dairies to achieve their environmental goals.
“Most of the carbon dioxide generated in dairy production originates from the stages before the milk even arrives at the dairy,” Tielinen says. “That is why it is essential to not waste valuable milk in the dairies’ processing operations. If milk-based products are lost in a dairy, a replacement amount of milk will have to be produced and transported to the dairy, which will produce even more carbon dioxide emissions.”