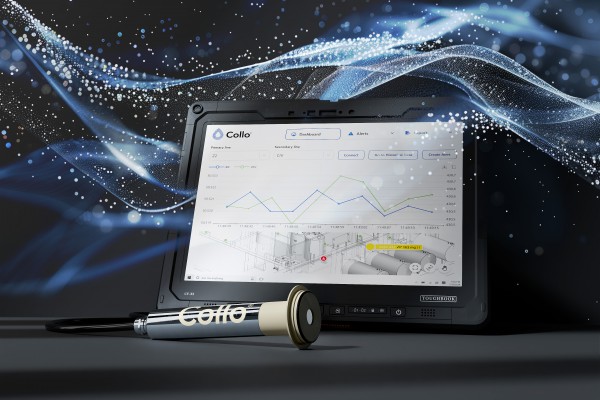
Courtesy of Collo
- Product loss in dairy processing is becoming a pressing concern as companies in the EU are required to report for the EU CSR Directive for the first time in 2025
- More stringent regulatory requirements and changing consumer preferences are powerful incentives for dairy companies to reduce product loss
- Product loss in push-out processes can be prevented by more accurate detection of the contents in the pipeline. This can be achieved using dielectric detection
As dairies scramble to meet sustainability targets ahead of the first year of reporting for the EU CSR Directive, the significant losses in push-out processes have been identified as low-hanging fruit by many companies.
From 2025, listed companies in the EU with more than 500 employees will be required to report sustainability information according to the new mandatory European Sustainability Reporting Standards (ESRS). This requirement will be expanded over the coming years to cover further categories of companies.
Product loss is a significant problem at many dairies and can greatly impact the carbon footprint. Hundreds of litres of product are often lost to the drains when liquid product is displaced with water by pushing it from one processing step to another. Frequently, as much as one percent of dairy production can be wasted in the push-out between product batches. For an average dairy plant processing 250,000 tons of raw milk annually, this means a loss of 2,500 tons of raw milk, as well as unnecessary CO2 emissions upstream in the supply chain.
However, inaccurate measuring technologies frequently prevent operators from addressing this issue in an effective way, as it can be difficult to correctly identify the product that moves through the pipeline. However, with appropriate measuring technology, the end of one batch and the beginning of the next can be accurately located. If it is not, the small losses at each push-out point, of which there can be hundreds, accumulate and become significant by the end of the process.
Pipeline contents are commonly measured by one of the three technologies – flow meter, turbidity sensor or conductivity sensor. Flow meters estimate the arrival of the product at the push-out point based on the system flow rate; turbidity sensors monitor the interaction between a light beam and the liquid; and conductivity sensors operate by measuring the electrical conductivity of the liquid.
A fourth method is based on monitoring the dielectricity of the liquid, i.e. its ability to hold electric charge. This is achieved by using a sensor that accurately identifies the substance moving through the pipeline as a radiofrequency electromagnetic field is induced into the liquid. Different liquids have different dielectricity, making them distinguishable from each other, giving each liquid a unique fingerprint.
“Measuring the dielectric properties of the liquid provides significant advantages over traditional approaches. Flow meters have very low accuracy and turbidity sensors cannot distinguish transparent liquids, such as whey concentrate, from water, and become clogged by thick liquids, like cream. The electrical conductivity of milk-based products is close to that of water, which translates into low sensitivity for conductivity sensors when detecting product interfaces,” says Matti Järveläinen, CEO of Collo, a leading manufacturer of dielectric liquid analyzing systems.
“The dielectric sensor can detect any liquid, whether it is thin, thick, colored, colorless, opaque or transparent. This means that the same measuring technology can be applied across the dairy plant, while in the past the plant needed to select the sensor based on the type of liquids processed in each particular location,” adds Järveläinen.
“A solution that can be scaled easily across the plant has been our goal from the start. We use sophisticated machine learning techniques to quickly calibrate our system to new liquids. The result is actionable information, like percentage of water in the product, which is transferred to the plant automation system, enabling process optimization,” Järveläinen continues.
Collo sensors were recently installed in four locations in a dairy plant’s raw milk reception, processing 243 million litres of raw milk per year. The plant previously used flow meters to control the push-outs. However, due to their low accuracy, what appeared to be optimal timing actually resulted in losses amounting to 600,000 litres per year. With the far higher accuracy of the dielectric sensor, 108 times better than the flow meter, losses were reduced to just 5,000 litres per year – a reduction of more than 99 percent.
The dairy has now decided to introduce Collo’s solution throughout the plant and automate the process.
Large dairy and other food producers are currently increasing their efforts to reduce their environmental impact ahead of environmental targets that loom in the near future, mainly in 2025 and 2030. Most of the greenhouse gas emissions caused by dairy operations originate at the farm. For instance, Nestlé, in its sustainability report, outlines how just five percent of its greenhouse gas emissions come from its operations, whereas 95 percent is made up of emissions in the supply chain. Raw milk production is the largest single source of emissions in dairy production, which any waste of milk-based raw material needs to be prevented and, preferably, eliminated.
Other companies have similar targets. Danone is committed to reducing its own greenhouse gas emissions by 47.2 percent by 2030 and those in the supply chain by 42 percent. Fonterra aims to reduce manufacturing emissions by 50 percent by 2030.
The year 2025 is an important milestone for many companies, as the 2030 Agenda for Sustainable Development was adopted by all United Nations members in 2015. Many companies set themselves 10-year targets at the time. The European Union is committed to implementing the UN Sustainable Development Goals, and the CSR Directive is one way in which the business community is made to play its part.
In addition to the regulatory requirements, changing consumer preferences is another powerful incentive for dairy producers to implement more eco-friendly production methods. A study by McKinsey and NielsenIQ found that products making claims related to sustainability have faster market growth – over a 5-year time span, such products grew about 18 percent more than the expectation was at the beginning of the period.
Waste in dairy processes needs to be reduced. Environmentally compatible processes are demanded by regulators and consumers alike. Wasting hundreds of litres of valuable product in every batch makes no sense when this can be prevented with the right technology. But it does not end there. With Collo’s versatile technology, we can help plants reduce water use too, an area which is also of keen interest to our customers and regulators alike. Working together with its customers, Collo can play a significant role in achieving a more sustainable dairy process, concludes Järveläinen.